Enhancing Manufacturing Efficiency with Light Source Technology in Industrial Applications
In recent years, the manufacturing sector has increasingly turned to innovative technologies to boost efficiency and productivity. One such innovation is "Light Source" technology, which has been recognized for its potential to revolutionize industrial applications. According to a report by the International Energy Agency (IEA), lighting accounts for approximately 15% of global energy consumption in industrial settings. As manufacturers face escalating energy costs and growing environmental regulations, the adoption of advanced light source technologies, such as LED and laser lighting, has become pivotal. These technologies not only reduce energy consumption but also enhance the quality of lighting, significantly impacting productivity and safety in manufacturing environments.
Moreover, a study by Research and Markets indicates that the global market for industrial lighting is projected to reach $30 billion by 2025, driven by the increasing demand for energy-efficient solutions. The integration of smart light source systems capable of real-time monitoring and automation can lead to substantial gains in operational efficiency. As industries strive to reduce waste and optimize processes, the role of light source technology will be crucial in shaping the future of manufacturing. This blog will explore how light source technology can enhance manufacturing efficiency and what implications it holds for the industry as a whole.
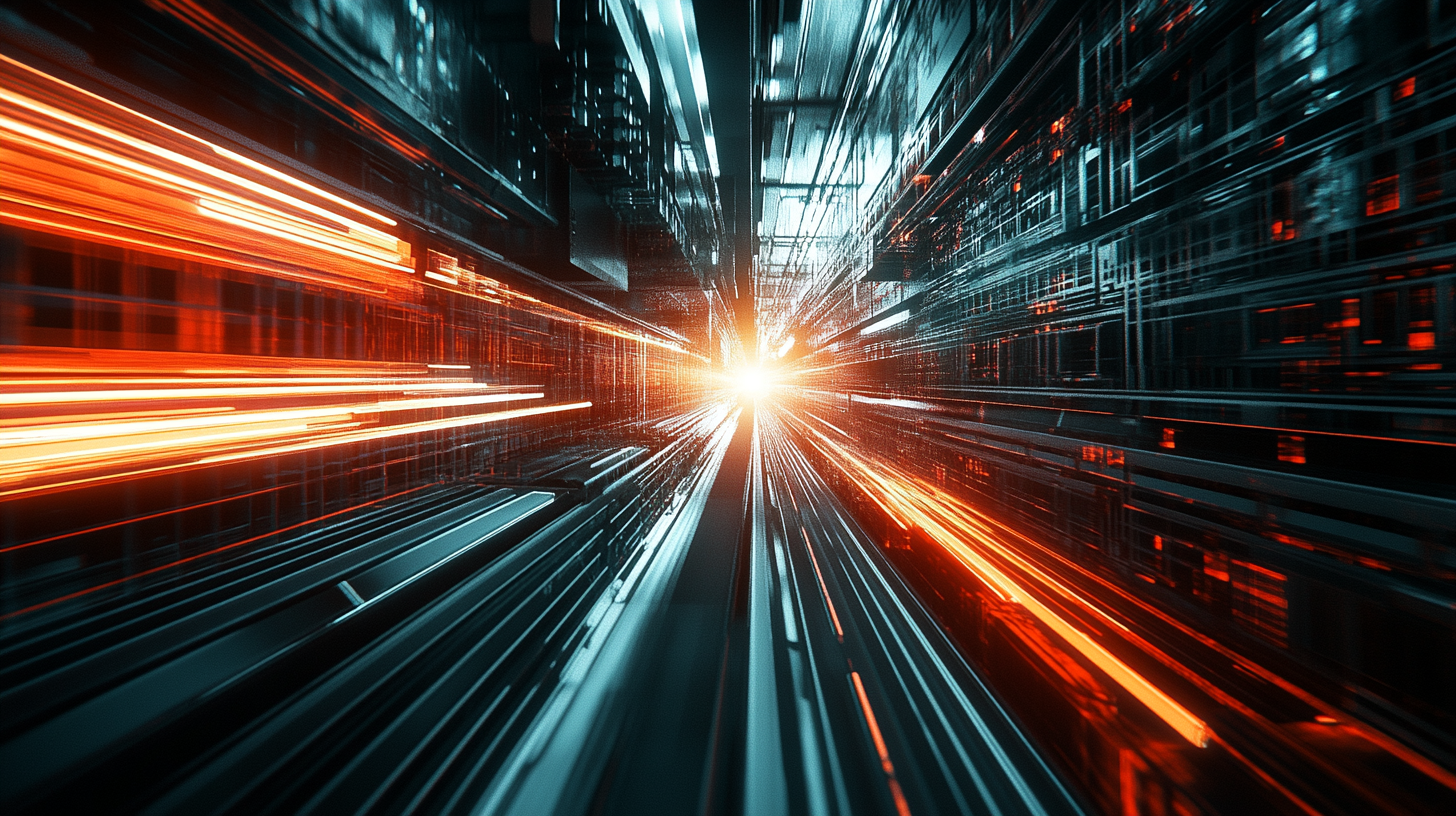
The Role of Advanced Light Source Technology in Manufacturing Optimization
Advanced light source technology is rapidly transforming the landscape of manufacturing optimization. In modern industrial applications, the integration of high-efficiency light sources, such as LEDs and lasers, plays a crucial role in enhancing productivity and product quality. These technologies not only improve the illumination of workspaces but also enable precise process control through improved visibility and reduced energy consumption. One significant advantage of using advanced light sources in manufacturing is their capacity for real-time monitoring and automation. By utilizing enhanced lighting systems equipped with sensors, manufacturers can track and analyze operational metrics efficiently. This data-driven approach allows for the continuous assessment of production processes, identifying bottlenecks and areas for improvement that were previously difficult to detect. As a result, manufacturers can implement timely interventions, reducing downtime and increasing overall throughput. Furthermore, the quality of the end product is significantly influenced by the lighting environment. High-quality light sources enable better visual inspection and quality control, ensuring that products meet stringent standards. By optimizing lighting conditions, manufacturers can reduce defects, enhance accuracy in manufacturing processes, and ultimately deliver superior products to their customers. As industries continue to embrace innovative light source technologies, the potential for manufacturing optimization will only grow, paving the way for smarter and more efficient production practices.
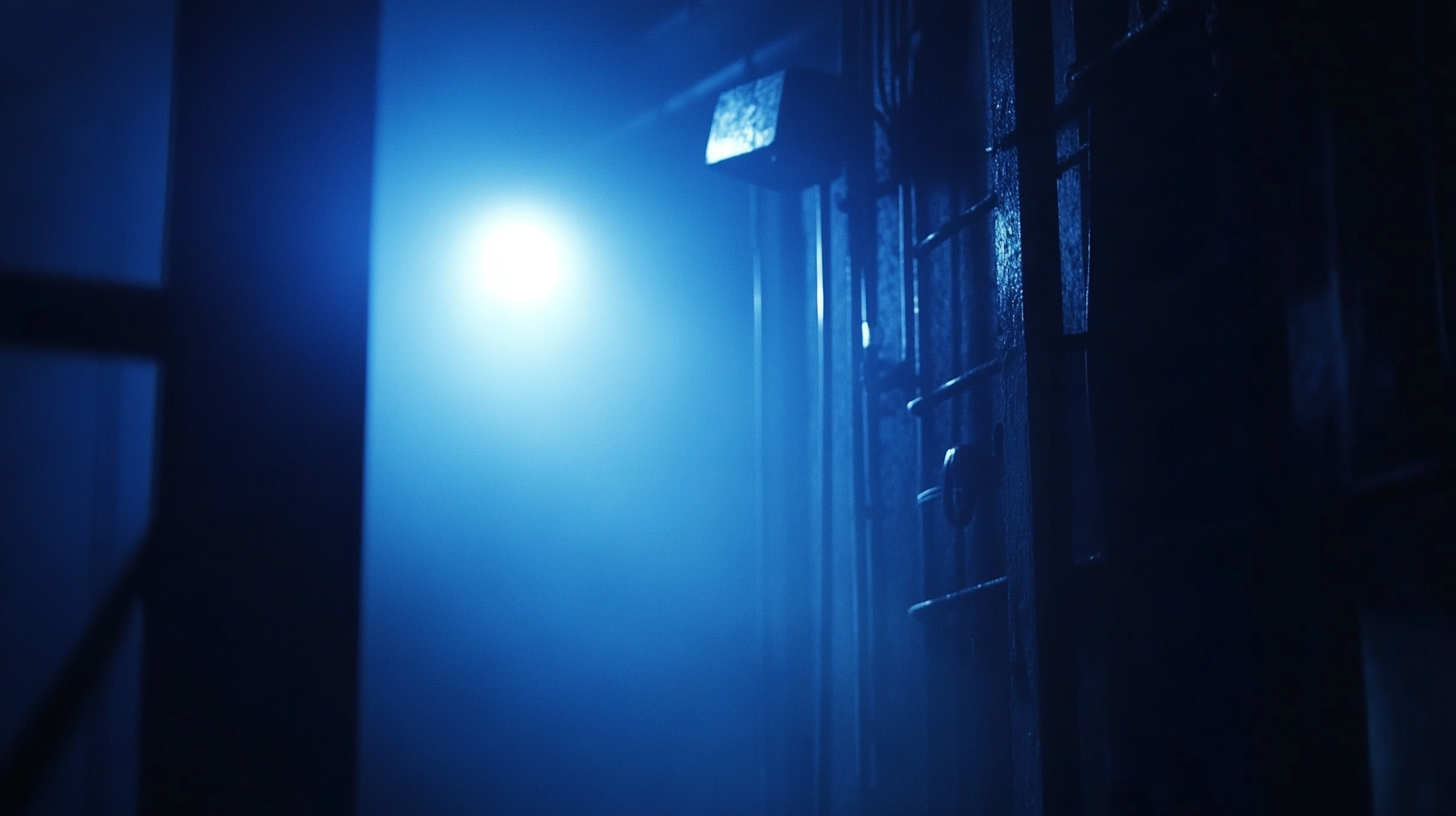
Key Benefits of Utilizing Light Sources in Industrial Processes
In today’s industrial landscape, the integration of advanced light source technology is revolutionizing manufacturing efficiency across various sectors. According to a recent report by the International Energy Agency (IEA), industrial lighting accounts for approximately 20% of total energy consumption in manufacturing facilities. By adopting energy-efficient LED systems, companies can reduce their lighting energy usage by up to 75%, translating into significant cost savings and reduced carbon footprints.
One of the key benefits of utilizing light sources in industrial processes is enhanced productivity. The right lighting levels can improve visibility, leading to a decrease in accidents and errors. A study by the Occupational Safety and Health Administration (OSHA) indicates that proper workplace illumination can reduce accidents by up to 30%, thereby positively impacting overall operational efficiency. Furthermore, advanced lighting systems can be equipped with sensors and automation features, allowing for dynamic adjustments based on real-time needs, further optimizing energy usage and operational workflow.
Another advantage is the potential for improved product quality. For instance, in the manufacturing of electronic components, precision tasks require optimal lighting to prevent defects. A report from the Lighting Research Center highlights that the use of high-quality light sources can significantly reduce the incidence of defects, leading to a 15% increase in overall product yield. This not only boosts profitability but also enhances customer satisfaction by ensuring consistent quality.
Overall, integrating modern light source technology into industrial applications not only fosters efficiency but also provides a pathway for manufacturers to remain competitive in a rapidly evolving market. By leveraging the advantages of advanced lighting, industries can achieve substantial improvements in both operational and product outcomes.
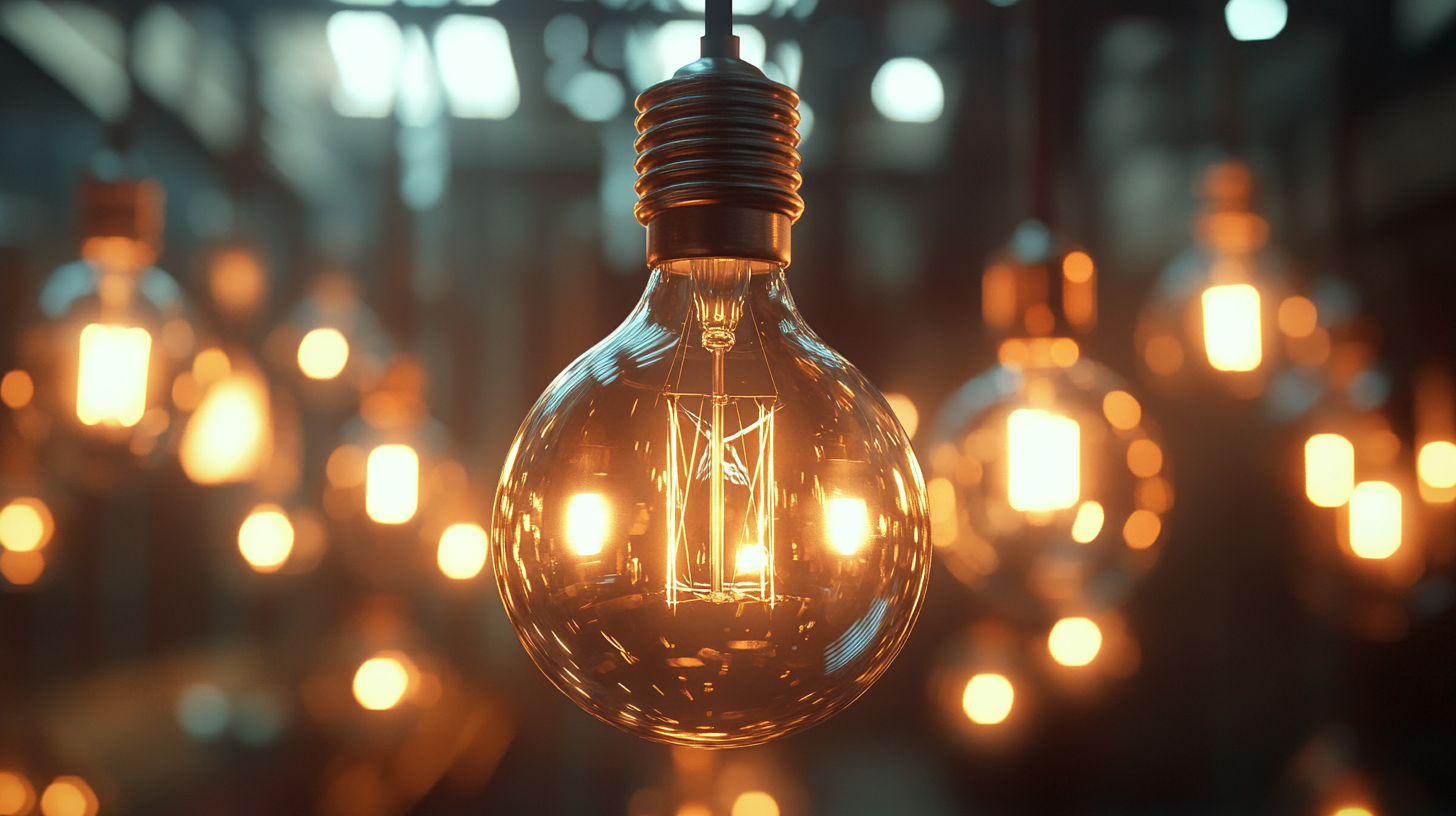
Case Studies: Successful Implementation of Light Source Technology
Light source technology is revolutionizing industrial applications by enhancing manufacturing efficiency across various sectors. Recent case studies have illustrated how companies are integrating this advanced technology to optimize operations. One notable example includes a recent report highlighting successful implementations of light source technology in shared economy enterprises, which serves as a testament to its transformative potential.
In manufacturing settings, precision and reliability are paramount. Utilizing advanced light sources, industries can achieve higher levels of accuracy in processes such as inspections and quality control. According to a 2021 report on shared economy developments, organizations that adopt innovative technologies, including those in industrial applications, can see an efficiency boost of up to 30%. Such improvements are crucial in today's competitive market, where resource conservation and cost reduction are top priorities.
Additionally, the integration of light source technology enables better energy management, leading to substantial savings. Data from industry analysts indicate that companies leveraging this technology can reduce energy consumption by nearly 25%, while also enhancing illumination quality for better working conditions. These advancements not only contribute to operational efficiency but also support sustainable practices within the manufacturing sector, further driving the motivation for adopting such technologies on a larger scale.
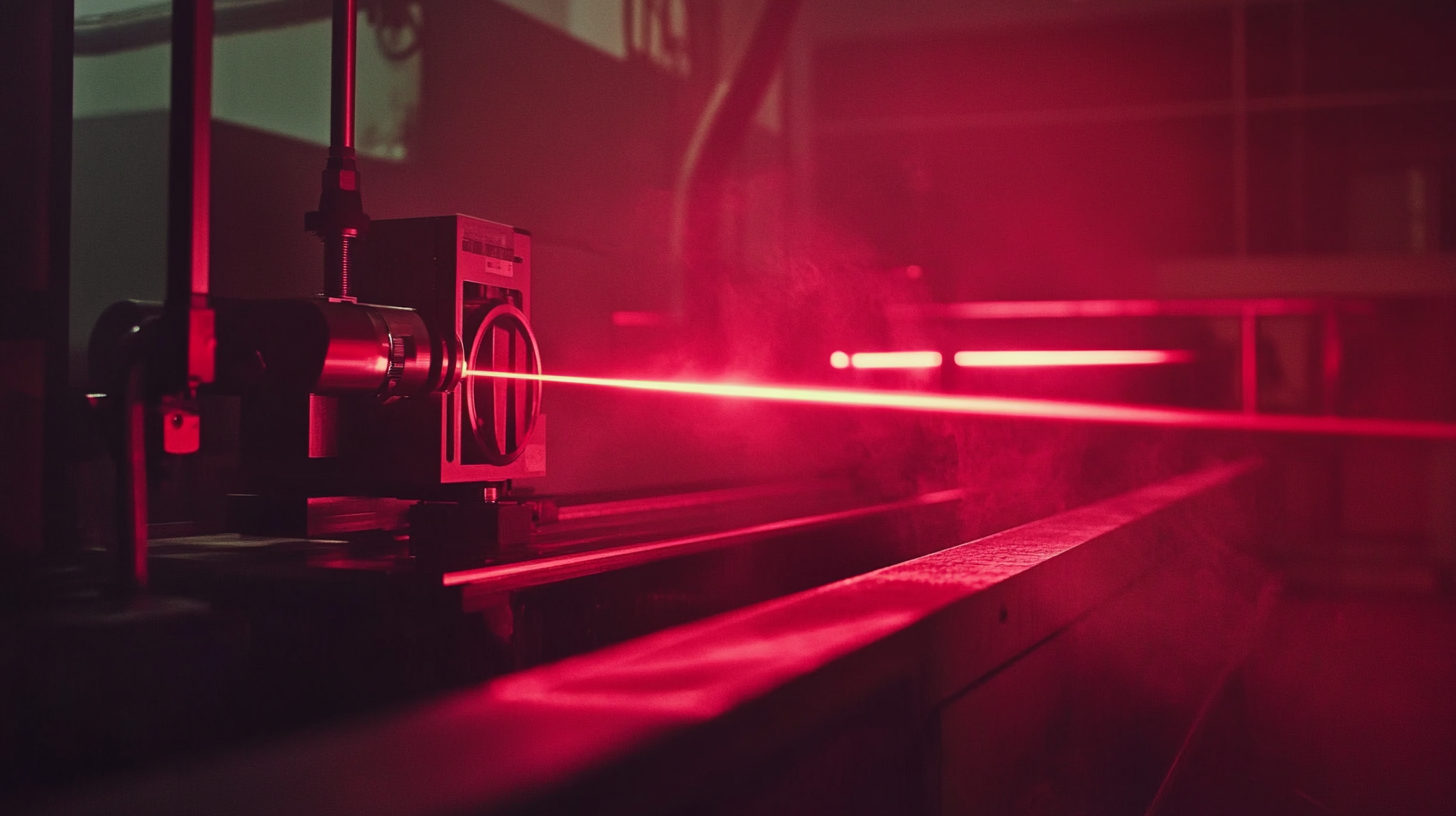
Comparative Analysis of Different Light Sources in Manufacturing
In the rapidly evolving landscape of manufacturing, the choice of light sources can significantly impact operational efficiency and productivity. A comparative analysis of different light source technologies reveals how advancements in illumination can optimize various industrial applications. Traditional incandescent and fluorescent lights are gradually being outperformed by modern alternatives such as LED and laser technologies, which offer enhanced brightness, reduced energy consumption, and longer lifespans. According to a report by the U.S. Department of Energy, converting from traditional lighting to LED can lead to energy savings of up to 75% in manufacturing plants, translating to substantial cost reductions.
When assessing the performance of light sources, factors like color rendering index (CRI), luminous efficacy, and maintenance costs play crucial roles. LEDs not only provide superior energy efficiency but also have higher CRI values, which improve visibility and color accuracy in processes requiring precise quality control. A recent industry survey indicated that manufacturers utilizing high-CRI lighting reported a 20% decrease in defects during production runs. Moreover, laser lighting technology, particularly in applications requiring high precision, is gaining traction. Reports suggest that lasers can improve alignment and assembly accuracy by over 30%, showcasing their effectiveness in high-stakes manufacturing environments.
The integration of advanced light source technologies is also influenced by the growing emphasis on sustainability within the manufacturing sector. As per the World Economic Forum, industries are increasingly pursuing eco-friendly initiatives, and switching to energy-efficient lighting aligns with global sustainability goals. This shift not only supports manufacturing efficiency but also plays a pivotal role in reducing carbon footprints, thus contributing to a more sustainable industrial ecosystem. As manufacturers continue to navigate these technological advancements, the comparative benefits of various light sources will undoubtedly shape the future of production environments.
Future Trends in Light Source Technology for Enhanced Efficiency
The landscape of manufacturing is on the brink of transformation, driven by advancements in light source technology. As industrial applications increasingly seek to optimize processes, the integration of innovative lighting solutions emerges as a pivotal factor in enhancing operational efficiency. Data from the International Energy Agency (IEA) suggests that lighting accounts for about 15% of global electricity consumption, indicating a significant opportunity for reduction through improved light source technologies.
Future trends in light source technology, particularly in the realm of LED and laser-based systems, are set to revolutionize the manufacturing sector. For instance, a study by the U.S. Department of Energy projected that widespread adoption of LED lighting could save approximately 190 terawatt-hours (TWh) of electricity annually by 2030—enough to power 24 million homes. These energy-efficient solutions not only reduce operational costs but also enhance visibility and accuracy in manufacturing processes, leading to lower defect rates and increased productivity.
Moreover, advancements in smart lighting systems equipped with sensors and IoT capabilities are paving the way for adaptive illumination. This technology allows manufacturers to tailor lighting conditions based on real-time needs, further improving energy savings and worker comfort. According to a report by ResearchAndMarkets, the global market for smart lighting in industrial applications is expected to reach $13.3 billion by 2026, reflecting a compound annual growth rate (CAGR) of 21.8%. As manufacturers harness these emerging technologies, they will not only foster sustainability but also position themselves competitively in an ever-evolving market.